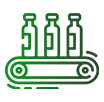
Heavy Duty Belting
Abrasion-resistant Rubber Belting
Abrasion-resistant rubber conveyor belting is designed to withstand wear and tear caused by the constant friction and movement of materials being transported. It is typically used in industries such as mining, quarrying, cement, and bulk material handling, where heavy, sharp, or rough materials are conveyed.
Abrasion-resistant rubber conveyor belts help in improving operational efficiency by reducing downtime due to belt wear, and they are a cost-effective solution for industries with demanding material handling needs.
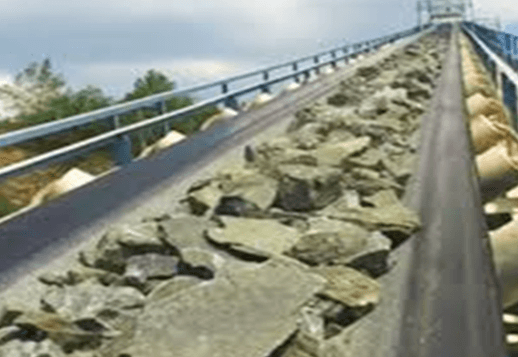
Key features of abrasion-resistant rubber conveyor belting include:
- Durability: Made from high-quality, abrasion-resistant rubber compounds that offer increased resistance to wear, ensuring longer service life and reduced maintenance costs.
- Tensile Strength: These belts are often reinforced with fabrics or steel cords for added strength, making them suitable for heavy-duty applications.
- Material Composition: The rubber used in abrasion-resistant belts is formulated with a higher proportion of hardwearing materials like carbon black, which enhances resistance to abrasion.
- Applications: Ideal for transporting bulk materials such as coal, sand, gravel, ores, and agricultural products.
- Temperature and Chemical Resistance: Some belts may also be formulated to resist heat, oil, or certain chemicals depending on the needs of the specific application.
- Customization: Available in different grades and thicknesses based on the material being transported and the level of abrasion resistance needed.
Fire Retardant Conveyor Belting
Fire Retardant Conveyor Belting is a type of conveyor belt designed to reduce the risk of fire hazards in environments where materials being transported or operational conditions pose a fire risk. These belts are typically used in industries such as mining, power plants, steel, cement, and grain handling, where fire safety is critical.
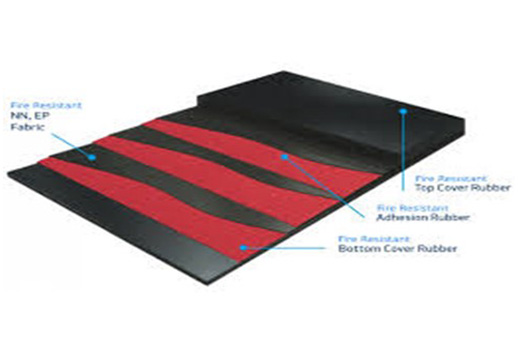
Key Features of Fire-Retardant Conveyor Belts:
- Fire-Resistant Properties: The belt materials are specially treated to resist ignition and reduce flame spread.
- Low Smoke Emission: In the event of a fire, these belts emit minimal smoke, reducing hazards to personnel and equipment.
- Anti-Static Properties: Prevents the buildup of static electricity, which can lead to sparks and ignition.
- Durability: Designed to withstand abrasive materials and harsh operating conditions.
- Compliance with Standards: Typically meet safety standards such as ISO 340, DIN 22103, or MSHA for fire resistance in conveyor belts.
Types of Fire-Retardant Belts:
- PVC Conveyor Belts: Commonly used in underground mining applications for coal and other materials.
- Rubber Conveyor Belts: Suitable for above-ground operations with added fire-resistant compounds.
- Fabric Conveyor Belts: Typically made with synthetic materials treated for fire retardance.
- Steel Cord Belts: Incorporates steel cords with fire-resistant rubber for strength and safety.
Applications:
- Underground Mining: Ensures safety in coal mines where flammable gases and materials are prevalent.
- Power Plants: Safeguards against fire hazards during coal or biomass transportation.
- Grain Handling: Reduces fire risks from dust explosions.
Food Grade Rubber Belting
Food-grade rubber conveyor belting is specifically designed to meet the strict standards required for use in food processing and handling applications. These belts are made from materials that are safe, durable, and resistant to common challenges in the food industry, such as moisture, oils, fats, and temperature variations. Here’s an overview
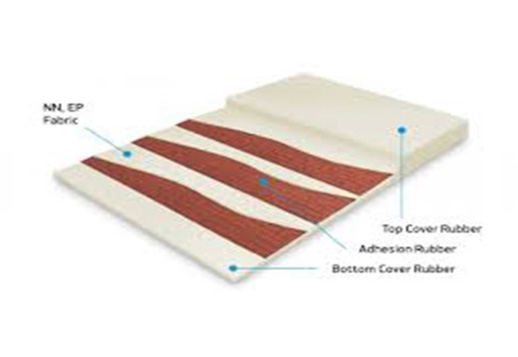
Key Features:
- Food Safety Compliance: Certified to meet FDA, EU, or other international food safety standards.
- Non-toxic Materials: Made from materials that are free of harmful chemicals, ensuring no contamination.
- Durability: Resistant to abrasions, tears, and wear, even under heavy-duty use.
- Temperature Resistance: Can operate in a wide range of temperatures, from freezing to high heat.
- Easy Cleaning: Designed for quick and effective cleaning to maintain hygiene standards.
- Chemical Resistance: Resistant to oils, fats, and chemicals used in food processing.
- Flexibility and Traction: Offers excellent flexibility and grip for efficient product movement.
Common Applications:
- Food Processing: Meat, poultry, seafood, baked goods, and dairy.
- Packaging: Conveying packaged food items.
- Agriculture: Moving fruits, vegetables, or grains.
- Beverage Industry: Conveying bottles, cans, or cartons.
Types of Food-Grade Rubber Belts:
- Smooth Belts: Ideal for general food handling applications.
- Inclined Belts: Feature textured surfaces or cleats for inclined conveying.
- Oil-Resistant Belts: Used in environments with exposure to animal fats or cooking oils.
- Heat-Resistant Belts: Suitable for high-temperature applications like baking or frying.
Multi-ply Textile Reinforced Carcass Conveyor Belting
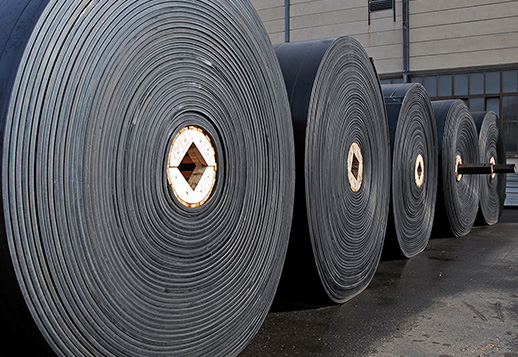
Strength ratings from 200 kN/m through to 3150 kN/m. The carcass has a minimum of 2 plies and maximum of 6 plies with impact absorbing layers of resilient rubber between plies. Protection to the carcass is achieved by hard wearing rubber covers of variable thickness from 1 mm to 20 mm to suit the application. The rubber covers are available in a wide range of compound formulations that meet even the most demanding specifications.
Heat Resistant Conveyor Belting
Heat Resistant Rubber Textile Conveyor Belts are highly resistant to hot cement, steel or sand material. The cover of this kind transport belts comprises of a unique rubber compound with high adhesive resistance, cut strength, high elongation at break and outstanding thermal protection.
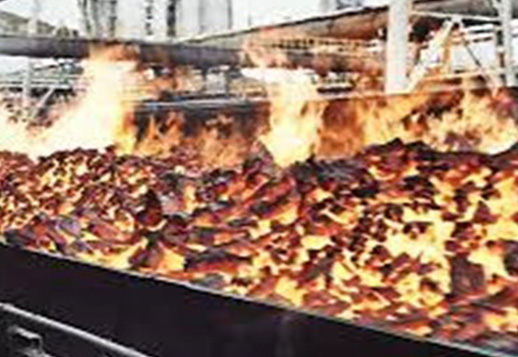
HR 100 Features:
- Temperature range of material: less than 200°C
- Temperature range of belt surface: 80°C – 100°C
- Cover rubber: SBR
Heat resistant grade has a premium quality SBR rubber compound with a very good abrasion and heat resistance to handle hot materials up to 200°C. This grade of belting is highly resistant to a variety of heat applications and gives good service for iron ore pellets, sand, castings, coke, limestone etc.
HR 150 Features:
- Temperature range of material: 150°C – 350°C
- Temperature range of belt surface: 100°C – 150°C
- Cover rubber: EPDM
HR grade has a hot belt compound of ethylene propylene rubber giving excellent heat resistance designed to carry hot materials without cracking. This grade of belting is most suitable for powdery materials such as cement products, fine limestone, clay, slag, steel millings etc.
HR 200 Features:
- Temperature range of material: 150°C – 450°C
- Temperature range of belt surface: 120°C – 180°C
- Cover rubber: EPR
HR-200 grade is the highest quality conveyor belting available for maximum heat resistance. This grade of belting is specially formulated EPR (ethylene propylene rubber) which provides superior heat resistance and ply adhesion for carrying hot cement clinker, phosphate, hot sintered ore and hot chemical fertilisers etc.
Oil-Resistant Rubber Belting
Oil-resistant rubber conveyor belting is designed for industrial applications where the belt is exposed to oil, grease, or other petroleum-based substances. These belts are engineered with materials that resist swelling, deterioration, and loss of tensile strength caused by oil contact. Here’s an overview:
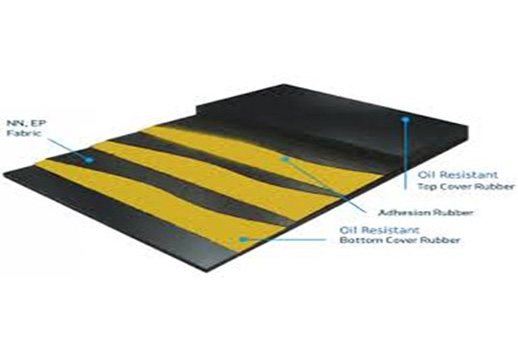
Key features:
- Oil Resistance: Specially formulated rubber compounds prevent absorption and degradation from oils and greases.
- Durability: High resistance to wear and abrasion for extended service life.
- Flexibility: Maintains flexibility even in challenging environments.
- Heat Resistance: Often combined with heat-resistant properties for operations involving high temperatures.
- Low Elongation: Ensures minimal stretching for efficient performance.
Types of Oil-Resistant Belts:
- MOR (Medium Oil Resistant): Suitable for materials with moderate oil content, such as grains or wood chips.
- SOR (Super Oil Resistant): For handling high-oil-content materials like oily grains, crushed soybeans, and foundry sand.
Applications:
- Food processing (handling oily food items).
- Recycling industries.
- Timber and woodworking operations.
- Mining and quarrying.
- Chemical plants.
- Automotive assembly lines.
Material Composition:
- Rubber Covers: Nitrile Butadiene Rubber (NBR) or similar oil-resistant rubbers.
- Reinforcements: Polyester, nylon, or steel cords for added strength and stability.
Advantages:
- Reduces downtime and maintenance caused by belt failure.
- Enhances operational safety.
- Suitable for various industrial conditions.
Steel Cord Conveyor Belts
Belting Supply supplies leading steel cord reinforced conveyor belts that are used in the mining and construction industries for transporting large volumes over long distances. These belts ensure optimal performance under the harshest operating conditions.
All Belting Supply, steel cord conveyor belts can be cut and spliced according to your specifications and come with a range of top and bottom cover compounds that protect your conveyor belt investment from fire, oil, abrasion and heat.
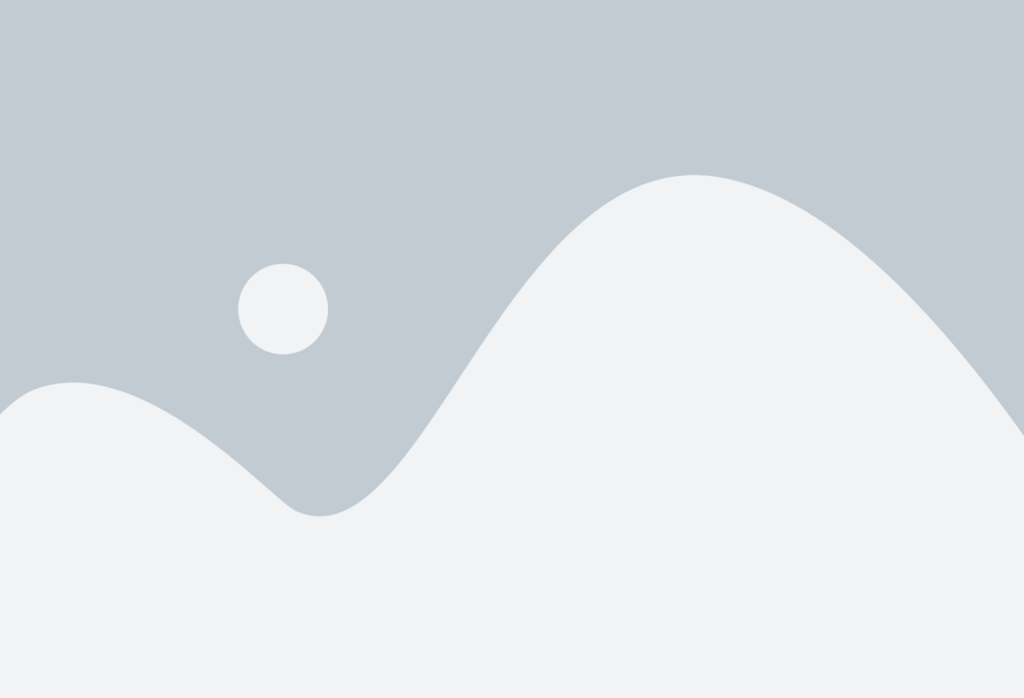
Features:
- High tensile strength up to 8 000 kN per metr
- Available in widths of up to 2.4 metres
- Roll lengths of up to 700 m depending on specification
- Large stock for a quick turnaround
- 12-month warranty on all conveyor belts
- Wide range of accessories available
- Comprehensive conveyor belt services
Rollers and Idlers
At Belting Supply Services, we provide a comprehensive selection of rollers and idlers that are essential for efficient conveyor system operations. Our range includes both trough idlers and pulley lagging solutions, designed to enhance the functionality and lifespan of conveyor belts. Trough idlers, the most common type of carry idler, are available in designs with 3 or 5 rollers. The 5-roll idler is engineered for a more uniform cross-section, enhancing carrying capacity, while the 3-roll design features a center idler roll flanked by wing idlers, optimizing support and reducing belt stress.
Ideal for a variety of industries, our rollers and idlers support conveyor belts in mining, agriculture, and manufacturing, ensuring smooth and reliable material transport. Coupled with our pulley lagging products, which are crafted to prevent belt slip and reduce wear, Belting Supply Services offers complete solutions that improve the efficiency and durability of your conveyor systems.
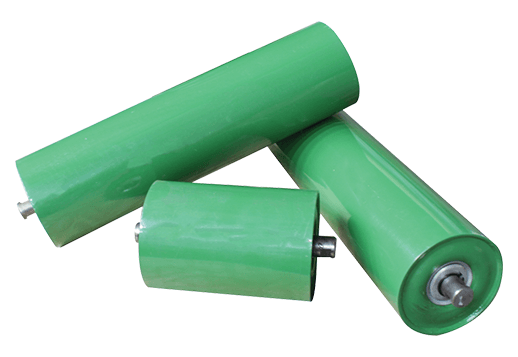
Rollers and Idlers
Belting Supply Services provides a range of Rollers and idlers. Trough idlers are the most common type of carry idler, which are typically designed with 3 or 5 idler rollers and are fitted to the carry-side of the conveyor belt. The 5-roll idler offers more uniform cross section, resulting in a greater net carrying capacity. The 3-roll design has a centre idler roll and wing idlers on either side.
Application:
- Conveying of various products including food and beverage industry.
- The benefit of using a trough idler is that they help to ensure the load-bearing capacity of the conveyor belt is the same along the length of the belt. With a more even distribution of load-bearing, the maximum capacity of material at the loading point won’t fall off of the belt.
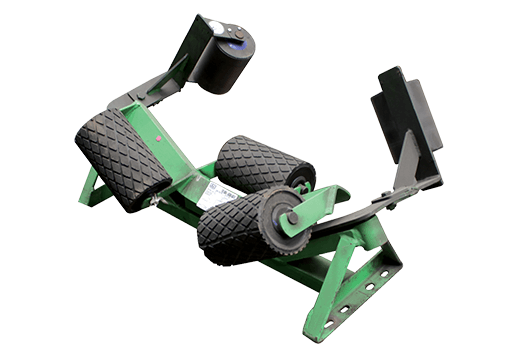
Pulley Lagging
At Belting Supply Solutions, we offer a range of pulley lagging tapes and other rubber products designed to enhance the performance and durability of your conveyor systems. Our solutions help prevent belt slip, reduce wear, and extend the life of your equipment.
Application:
Increase friction on drive pulleys and skirting rubber to reduce spillage at loading points.
Key Features:
Pulley Lagging Tapes
- With or Without Profiles: Available with or without profiles to suit your specific application needs.
- Increased Coefficient of Friction: Rubber lagging tapes are designed to increase the coefficient of friction between the belt and pulley, effectively preventing belt slip.
- Durability: Enhances the lifespan of your pulleys and reduces maintenance costs.
Slide Lag Pads and Retainers
- Easy Installation: Slide lag pads and retainers provide a quick and efficient solution for pulley lagging, offering easy installation and replacement.
- Improved Performance: These pads help improve belt grip and reduce wear on the pulley surface.
Skirting Rubber
- Sealing Solution: Skirting rubber is essential for preventing material spillage at transfer points on conveyor systems.
- Durability: Made from high-quality rubber, it is designed to withstand harsh conditions and reduce maintenance.
Rubber Repair Strips
- Quick Repairs: Rubber repair strips provide a fast and effective solution for repairing damaged conveyor belts.
- Strong Bond: Ensures a durable and long-lasting repair, minimizing downtime and extending the belt’s lifespan.
Steel Idlers
A steel idler troughing frame is a structural component used in belt conveyor systems to support and guide the conveyor belt. It consists of steel frames designed to hold idler rollers in a troughing configuration, which is typically angled to help form the belt into a trough shape. This trough shape ensures efficient material containment and transportation.
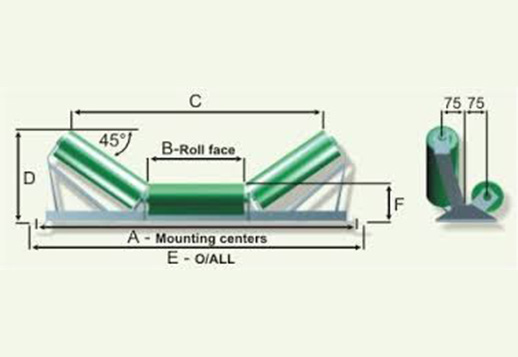
Components of a Steel Idler Troughing Frame:
- Steel Frame: The structure that holds the rollers in place and mounts them onto the conveyor system.
- Troughing Rollers: Usually three rollers are mounted—one horizontal and two inclined at angles (typically 20°, 35°, or 45°).
- Mounting Points: These allow the frame to be securely attached to the conveyor structure.
Functions:
- Material Support: Helps form the belt into a trough to carry bulk materials efficiently.
- Load Distribution: Provides even distribution of the load across the belt.
- Alignment: Maintains proper alignment of the conveyor belt during operation.
Applications:
- Mining
- Quarrying
- Cement plants
- Power plants
- Bulk material handling systems
Rubber Conveyor
This is a general-purpose, versatile conveyor belt that is suited to conveying bulk materials of all types. It can be joined endlessly by familiar hot or cold vulcanising processes or using mechanical fasteners. Strength ratings from 200 kN/m through to 3150 kN/m. The carcass has a minimum of 2 plies and a maximum of 6 plies with impact-absorbing layers of resilient rubber between plies. Protection to the carcass is achieved by hard-wearing rubber covers of variable thickness from 1 mm to 20 mm to suit the application. The rubber covers are available in a wide range of compound formulations that meet even the most demanding specifications.
We stock a wide range of rubber conveyor belting, from your light specs(Class 250) up to your heavy specs. (Class 800). We also manufacture rubber belts in our workshop, (Steep Incline and Magnetic cleated conveyors). We supply rolls of belting and cut lengths as per customer requirements. We service the mining sector
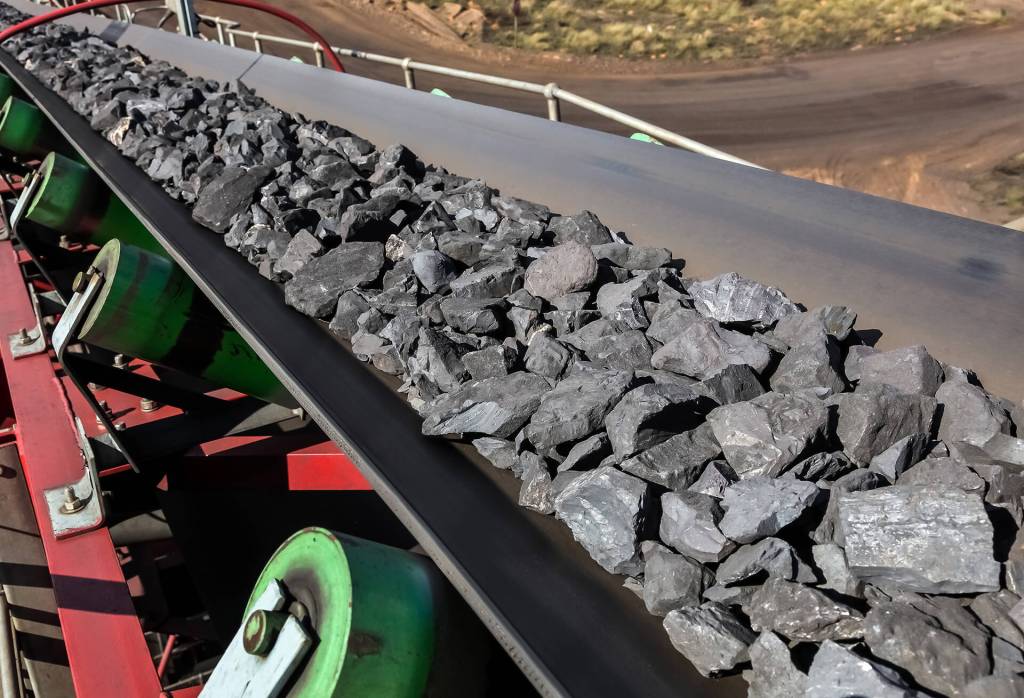
Rubber Conveyor
At Belting Supply Solutions, we stock a comprehensive range of rubber-covered conveyor belting designed to meet the demands of various industries. Our belting options are versatile, durable, and can be customized to suit your specific requirements.
Application:
- Stockists of slab rubber-covered conveyor belting, available in Class 250/2 to 1000/4 with Grade N covers in various thicknesses to accommodate a wide range of applications.
- Heat-resistant covers capable of withstanding continuous temperatures up to 200°C and intermittent temperatures up to 400°C.
- All belting is cut to meet specific requirements.
Special classes and covers are available upon request for tailored applications.
Additional Information:
Conveyor belts have been in use since the 19th century. In 1892, Thomas Robins began developing a series of inventions that resulted in the creation of a conveyor belt designed for transporting coal, ores, and other products. By 1901, Sandvik had invented and started producing steel conveyor belts. Richard Sutcliffe’s 1905 invention of conveyor belts for coal mines transformed the mining industry. In 1913, Henry Ford introduced conveyor-belt assembly lines at the Ford Motor Company’s Highland Park factory in Michigan. In 1970, Intralox, a company based in Louisiana, registered the first patent for all-plastic modular belting.
A belt conveyor system comprises two or more pulleys with an endless loop of the conveyor belt that rotates around them. One or both pulleys are powered, moving the belt and the materials on it forward. There are two primary industrial categories of belt conveyors: those used for general material handling, such as moving boxes within a factory, and those for bulk material handling, like transporting large volumes of grain, salt, coal, ore, and sand.
In industrial environments, conveyors often include tripping mechanisms such as trip cords along their length, allowing workers to shut down the conveyor immediately in case of an issue. Warning alarms are also installed to alert employees when a conveyor is about to start. In the United States, the Occupational Safety and Health Administration (OSHA) has established regulations for conveyor safety, specifically OSHA 1926.555.
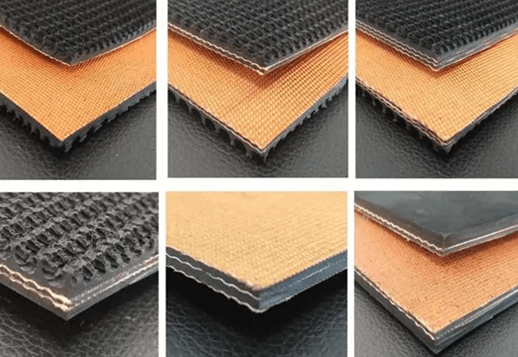
Rubber Roughtop Belting
Belting Supply Solutions offers a versatile range of roughtop and multipurpose belting designed for conveying packed goods and power transmission. Our belting products are engineered for durability and performance across various industrial applications, ensuring reliable operation whether on flat or inclined surfaces.
Application:
- Rough top conveyor belt comprise two or three ply with cut edges, carcass of NN/EP fabric , With the top covers made using wear-resistant rubber featuring non-slip surface, used for transporting light weight goods, such as sacks, boxes and parcels, on Inclined surface at angles of 35°.
- Bareback rough top belt allows less possibility of friction thus making these suitable for running over table as well as flat panel.
- Rough top conveyor belt is specially designed for this purpose and has either a ridged rubber surface on top and bare back fabric/ regular rubber back.

Multipurpose (Bare Back) Belting
Bare Back Conveyor Belting is designed specifically for handling lightweight materials efficiently. It operates smoothly on steel, wood, or other low-friction surfaces, known as sliding beds, thanks to its low-friction back and top covers. Compared to standard belting, Bare Back Conveyor Belting boasts a lower friction coefficient between the belt and the framework. This feature significantly reduces wear on the conveyor belt while maximizing operational efficiency, making it an ideal choice for applications requiring reliable and smooth material transport.
Application:
Bare Back Conveyor Belting is versatile and ideal for a range of industries, including the automotive, rubber, and woodworking sectors. It excels in environments such as recycling plants and scrap material processing facilities, where efficient and smooth transport of lightweight materials is essential. The low-friction design allows for seamless operation across various surfaces, making it a reliable choice for handling diverse applications while minimizing wear and enhancing productivity.
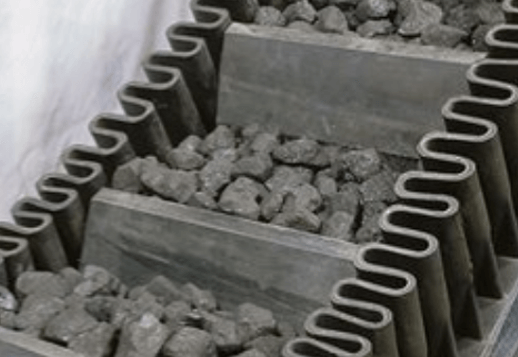
Steep Angle Belting
Belting Supply Solutions offers specialized steep angle belting designed for efficient conveying on inclines up to 90 degrees. Our steep angle belts are engineered to provide maximum performance and reliability, even in the most challenging environments.
Application:
- Pocket Type Belting: Equipped with sidewalls and cleats for steep incline conveying up to 90°. Features top-quality rubber sidewalls up to 400mm high and T, C, and TC cleats up to 360mm, with a cross-stabilized base belt for maximum conveying performance.
- Special classes, grades, and profiles can be imported upon request.
- Belt selection calculations are available through our technical department for optimal performance.
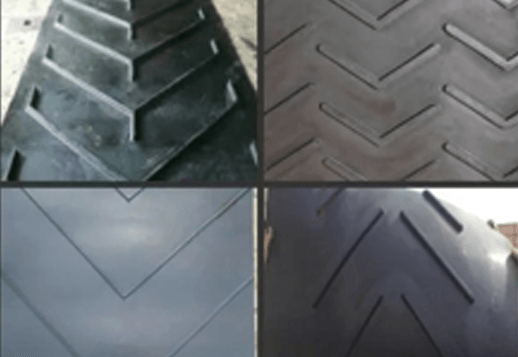
Chevron Belts
Chevron belts are specially designed conveyor belts featuring a distinctive V profile or paddle profile that enhances their ability to transport materials efficiently. These belts are constructed without joints in the carcass, ensuring a seamless design that contributes to a longer service life. The cleats and top cover rubber are integrally vulcanized, providing exceptional durability and performance. Each cleat pattern, angle, and pitch is meticulously engineered to maximize material handling capabilities. Available in various types, including open V, closed V, and other specialized patterns, these belts offer different depths, ranging from 15mm to 25mm, to accommodate a wide range of applications, from high to medium load transportation.
Application:
Chevron belts are ideal for transporting bulk materials on inclined surfaces, making them a preferred choice in various industries. Their unique V profile allows for efficient movement of materials such as grain, coal, aggregates, and other loose products. These belts excel in environments where traditional flat belts may struggle to prevent material slippage, especially on steep inclines. Common applications include agricultural operations, mining, recycling facilities, and construction sites. With their robust design and versatile cleat patterns, Chevron belts ensure reliable performance and optimal material handling in challenging conditions.
Solidwoven PLK Belting
Our Solidwoven PLK belting is designed for durability and reliability in demanding industrial applications. This solid woven belting is ideal for use in bucket elevator systems and the general conveying of wood, bulk goods, and other materials in tough environments.
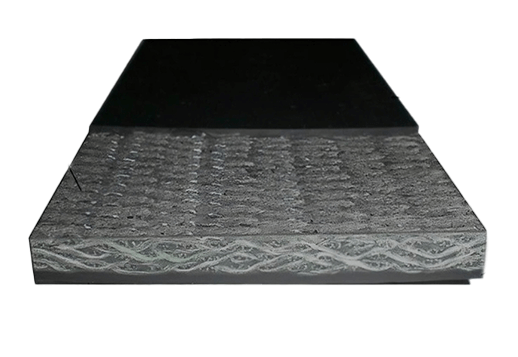
Solidwoven PLK Belting
Application:
Solid Woven Belting: Designed for bucket elevator applications and general conveying of wood and bulk materials, offering flame retardant properties for enhanced safety in demanding environments.
Contact Us
PVC, PU and Modular Conveyor:
Gauteng - Head Office
Our products
At Belting Supply Services, we provide an extensive selection of top-quality products designed for all industries. Our range includes conveyor belts, industrial hoses, and power transmission products, all sourced from leading manufacturers to ensure reliability and performance. Whether you need standard items or customized solutions, we have the products to meet your needs.